The Problem:
The tank is located in Monroe Township, NJ. Just southwest of New York City, NY. This area can be prone to harsher winter weather and below freezing temps. Below are issues that could arise on an uninsulated fire protection storage tank.
- Ice build-up within the tank
- Frozen water lines
- No access to emergency fire protection water supply
- Energy waste from tank heater
- Not meeting NFPA 22 freeze protection codes section 16.1-16.5.
How Was RIDGLOK® Selected?
The RIDGLOK® System was selected due to fire protection tanks requiring heaters. The use of the RIDGLOK® insulation system not only helps prevent freezing, but also helps conserve energy while working in conjunction with the heater.
They ultimately selected RIDGLOK®’s vertical standing seam insulation (VSSI) system because of past history, competitive price, and their long-standing experience working with RIDGLOK® insulation panels.
The manufacturer’s project manager knew he could rely on the system for:
- Quality thermal protection
- Speed of installation
- Safety of installation
- Low maintenance of the insulation system
- Long life of the insulation system
- High wind resistance
- Structural connections sealed against weather
- High level of corrosion protection against CUI (corrosion under insulation)
- Color Matching the facility’s color scheme
- Easy fast repairs
- Expansion/contraction built naturally into the system (no bands to be periodically checked and tightened)
- Quality resulting from panels pre-manufactured to specification
Before:
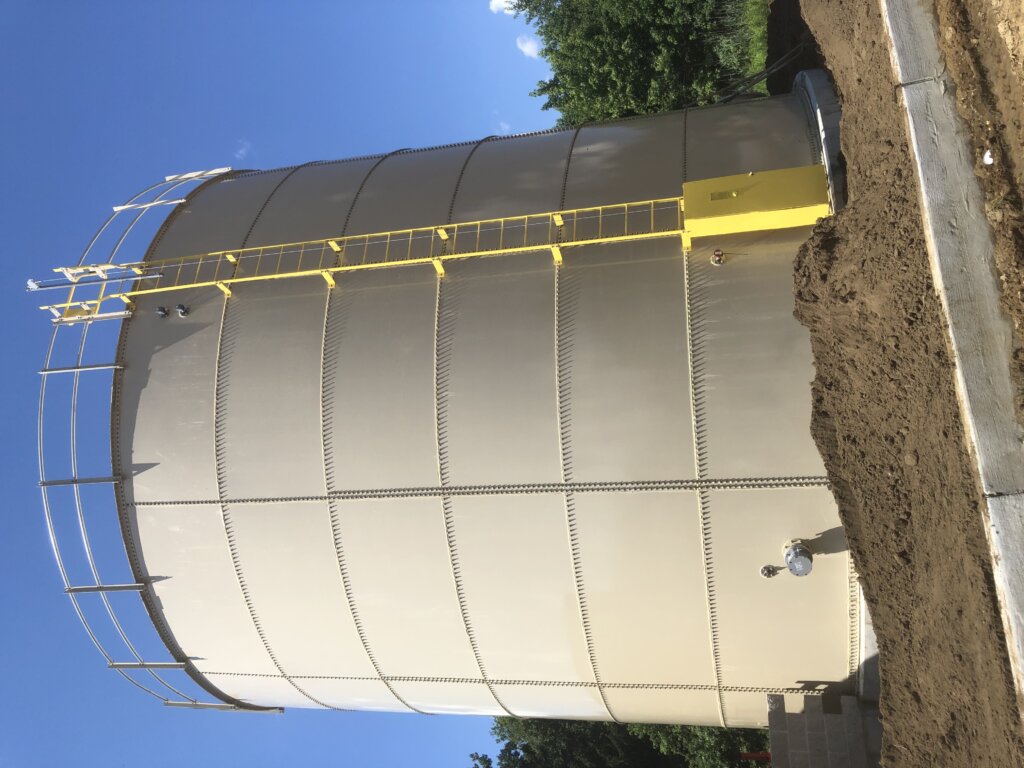
The Solution:
This RIDGLOK® Vertical Standing Seam Panel Insulation System was manufactured at the MC&I facility in Reed, KY for installation on a 31’W x 30’T fire water storage tank with a straight roof panel design. The tank shell and roof materials consist of 2” Polyisocyanurate insulation board R-Value of 13.1. Insulation is laminated to stucco embossed 0.024 x 24” W aluminum metal jacketing at our facility prior to installation. Also, the RIDGLOK® straight roof design and flashing system minimized potential corrosion points contributing to the overall performance of the system.
The Experience:
MCI RIDGLOK used the engineer’s input to address all of the customer’s concerns before even one piece was fabricated.
- The RIDGLOK system design allowed for minimal maintenance on the part of the end-user. The tank had only two protrusions for liquid ingress and egress, and an external ladder with four ladder clips. The end-user only needed to check caulking on these four protrusions once per year.
- Panels for the tank shell were custom designed to match the tank height.
- A roof system was designed to provide the client with a watertight roof and proven flashing details at the roof-shell interface.
- The shell and roof designs were designed for high-winds.
- Each panel consisted of a factory painted aluminum sheathing laminated to 2” of closed-cell polyisocyanurate insulation. This insulation is hydrophobic (repels and sheds water) and moves the water down and out of the exterior tank system. Water that backs up into the insulation panels during a flood, is repelled out nearly as fast as the water recedes.
The Result:
The client now enjoys:
- Lower Energy bills
- Aesthetically pleasing tank that complements the facility
- 1 year warranty and a Lifespan of 25+ years of thermal protection
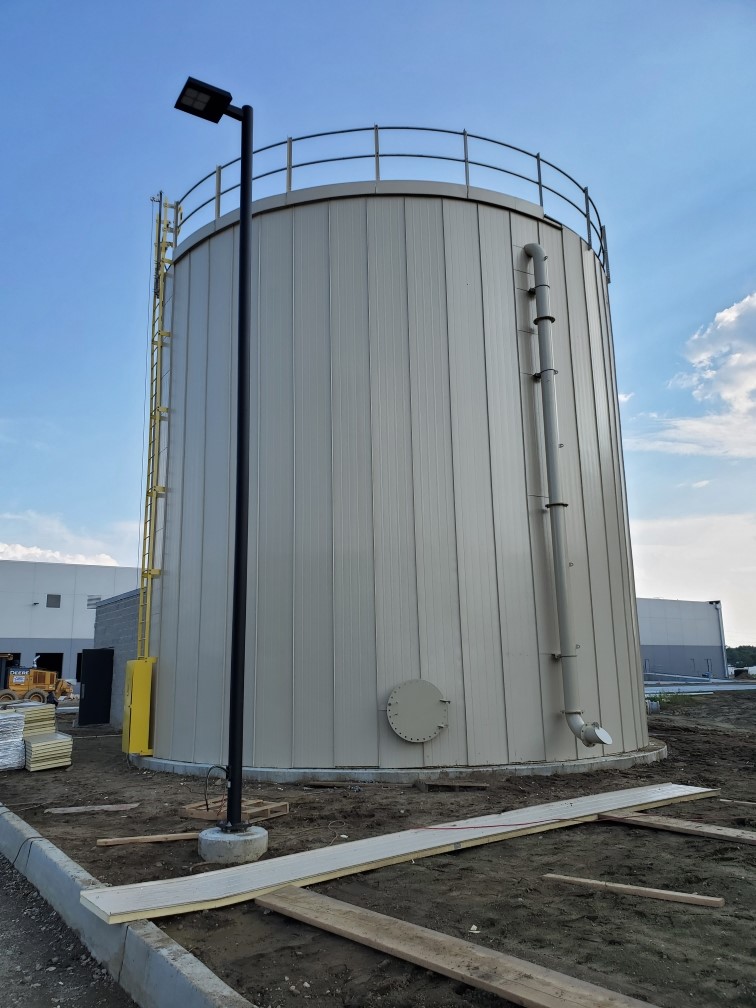
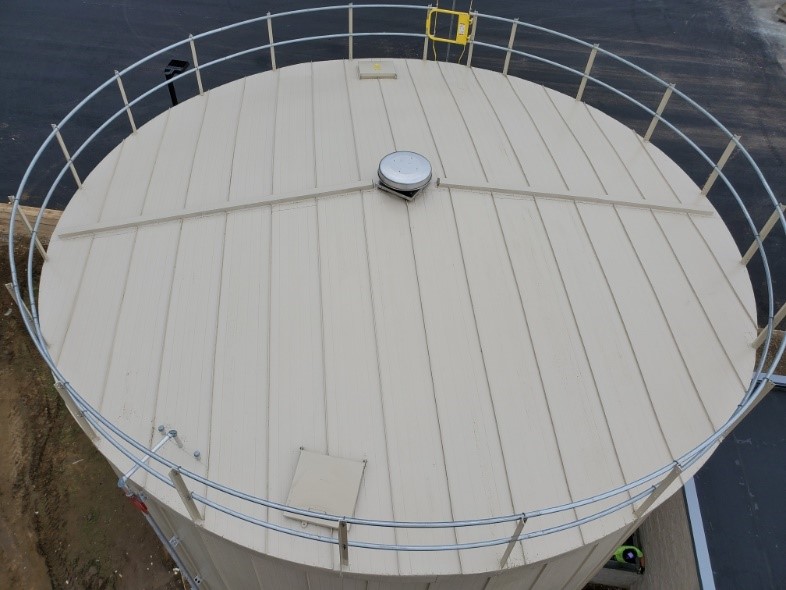
Testimonial:
Upon completion of the project, the inspector signed a completion form stating he would recommend MC&I and the RIDGLOK® Panel System. And that work was completed in a satisfactory manner.