Overview:
RIDGLOK® insulation system was installed on a fire water storage tank located at a tire manufacturing plant in Clarksville, TN. Clarksville is adjacent to Ft. Campbell, KY, and less than an hour from Nashville, TN.
The Problem:
Once erected and hydro-tested, such a tank in warmer climates is typically complete. Except, Tennessee is known to get a few freezes and snow each year, but insulating the tank will help with the following:
- Ice build-up within the tank
- Frozen water lines
- No access to emergency fire protection water supply
- Energy waste from the tank heater
- Not meeting NFPA 22 freeze protection codes section 16.1-16.5
How Was RIDGLOK® Selected?
In colder regions, storage tanks for fire protection require tank heaters. Without proper insulation, the cost of heating these tanks is prohibitive. NFPA 22 codes section 16.1-16.5 permit the use of tank insulation to CONSERVE energy.
The storage tank manufacturer trusts RIDGLOK®’s long history of protecting fire protection tanks. Having used it on projects for many years, they have complete confidence in this newer technology which is rapidly overtaking conventional insulation systems.
They ultimately selected RIDGLOK®’s vertical standing seam insulation (VSSI) system because of past history, competitive price, and their long-standing experience working with RIDGLOK® insulation panels.
The manufacturer’s project manager knew he could rely on the system for:
- Quality thermal protection
- Speed of installation
- Safety of installation
- Low maintenance of the insulation system
- Long life of the insulation system
- High wind resistance
- Structural connections sealed against weather
- High level of corrosion protection against CUI (corrosion under insulation)
- Color Matching the facility’s color scheme
- Easy fast repairs
- Expansion/contraction built naturally into the system (no bands to be periodically checked and tightened)
- Quality resulting from panels pre-manufactured to specification
Before:
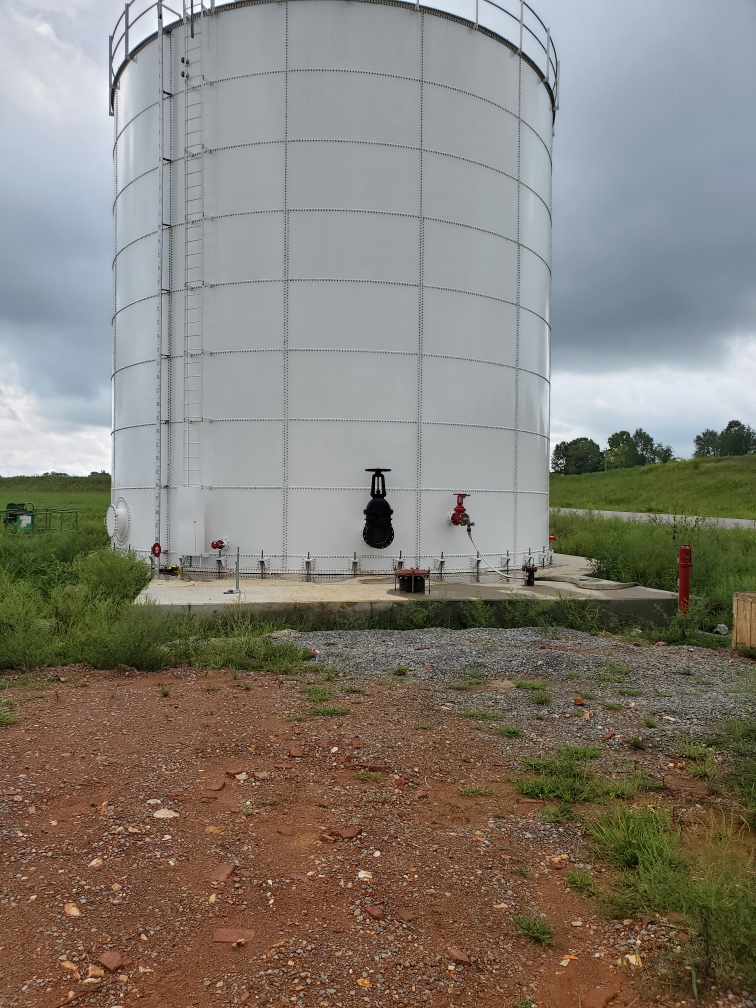
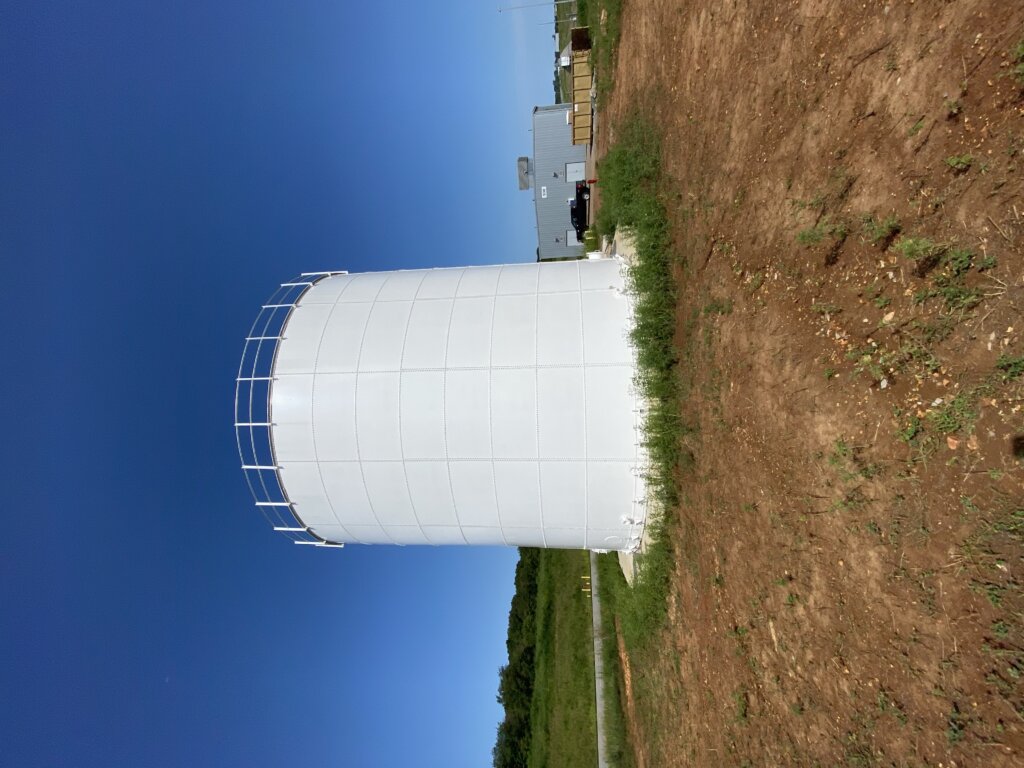
The Solution:
This RIDGLOK® Vertical Standing Seam Panel Insulation System was manufactured at the MC&I facility in Reed, KY for installation on a 40’D x 40.09’H fire water storage tank with a straight roof panel design. The tank shell and roof materials consist of a 2” Polyisocyanurate insulation board R-Value of 13.1. Insulation is laminated to stucco embossed 0.024 x 24” W aluminum metal jacketing at our facility prior to installation. Also, the RIDGLOK® straight roof design and flashing system minimized potential corrosion points contributing to the overall performance of the system.
The Result:

The client now enjoys:
- Lower Energy bills
- An aesthetically pleasing tank that complements the facility
- 1-year warranty and
- a lifespan of 25+ years of thermal protection
Testimonial:
Upon completion of the project, the inspector stated all work was completed satisfactorily and he would recommend MC&I and the RIDGLOK® Panel Systems. He also concluded with the install crew did a “Good Job” and was “Professional”.