MC&I designed, manufactured and installed the RIDGLOK® Vertical Standing Seam Insulated Panel System on two welded silos, located at a tank manufacturing facility before being shipped to Mars Chocolate North America in Topeka, KS for final silo installation.
One silo storage tank was a 10′ in diameter x 17.5′ in height, welded silo. The second silo was an 11.92′ in diameter x 40.33′ in height, welded silo. The silo insulation project was completed in December 2012.
The RIDGLOK® Vertical Standing Seam Insulated Panel System consisted of 0.024 stucco-embossed aluminum metal jacketing, in Fawn color, laminated to 3″ of polyisocyanurate insulation board (R-value of 20.3), using a straight pan roof system. The silos were insulated at the tank manufacturer before they were delivered to the customer. They were insulated while in the horizontal position, and then were transported by truck to the facility located in Topeka, KS.
There are multiple benefits to insulating agricultural storage silos, such as the sugar silos above. Insulation helps control condensation, which helps minimize mold & mildew. It also reduces freezing of the stored products in the silo, allowing for more even distribution of the product with the silo unloader. Insulation saves on monthly energy costs by conserving heating or cooling if the product requires it.
For Process control, insulation will protect the product from freezing or being heated by solar radiation. It will also reduce the cooling of the stored substance, which may prevent it from setting and remaining in a solid form. In both cases, additional heating or cooling may be required.
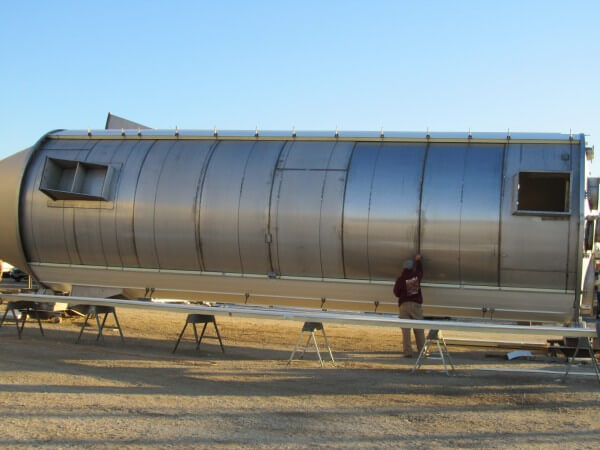
Silo Insulation Being Installed | RIDGLOK® Vertical Standing Seam Insulated Panel System Panels in Fawn Color
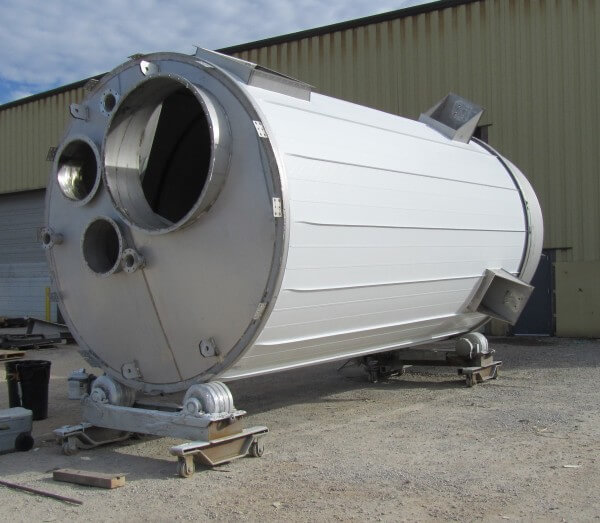
Sugar Silo | RIDGLOK® Vertical Standing Seam Insulated Panel System Installed Before Tank Erection