From purification to re-refining, reclamation to disposal, packaging to transportation, chemical brokerage to distribution, and project management to process optimization, ORG CHEM Group has the resources and determination to deliver innovative solutions.
The two welded tanks were 11.92’ in diameter x 35.5’ tall and were located very close in proximity to two other storage tanks with conventional insulation, making the working area quite challenging. Visually, you can see the differences on the exterior appearance of RIDGLOK® vs. Conventional Style Insulation, but the significant difference between the 2 styles of tank insulation is underneath the metal jacketing. The RIDGLOK® Panel Insulation System is connected to the tank by stainless steel cables that are tensioned on the tank with stainless steel strapping that is connected to the cables and also placed into the standing seam of the panels. With a double machine folded standing seam, the strapping connections are locked into the standing seam ridges creating a more durable system engineered to withstand up to 95 mph wind speeds. The connection system is also protected from the elements making the lifespan on the system 25+ years with no maintenance.
The RIDGLOK® Insulated Panel System consisted of 0.024 stucco-embossed aluminum metal jacketing in mill finish laminated to 1.5” of polyisocyanurate insulation board with an R-value of 9.6 using a cone roof design. The tanks were utilized for storage at the chemical facility. The project was completed on May 18, 2016.
RIDGLOK® Insulation Systems MINIMIZE heat gain and REDUCES the load on the chillers or heaters to maintain consistent operating temperatures. Chemical tanks are insulated for OPTIMAL process control. Insulation of storage tanks REDUCES routine maintenance and PREVENTS energy waste and LOWERS fuel costs.
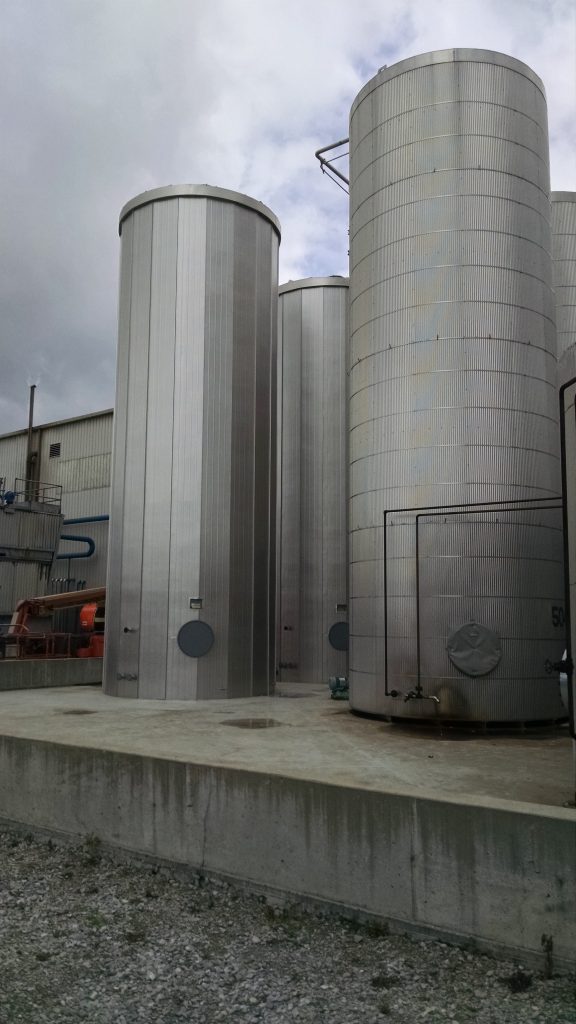
Chemical Industry – RIDGLOK® Tank Insulation on Left